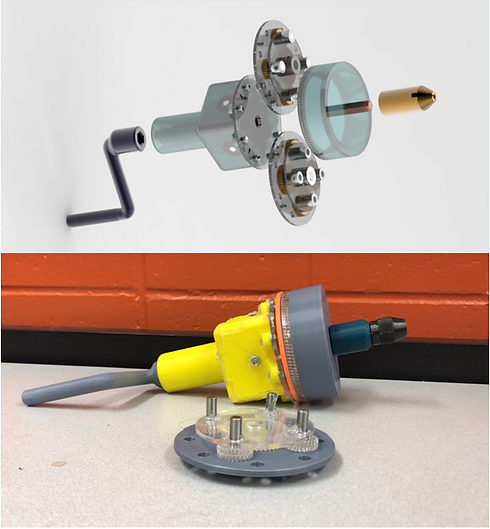
TEAM AB7_1
ME 270 Design For Manufacturability (DfM) Project
GET TO KNOW THE TEAM

JOEY BENNETT
Project Procurement Specialist
DEANDRE FRISBIE
Project Lead/Administrator
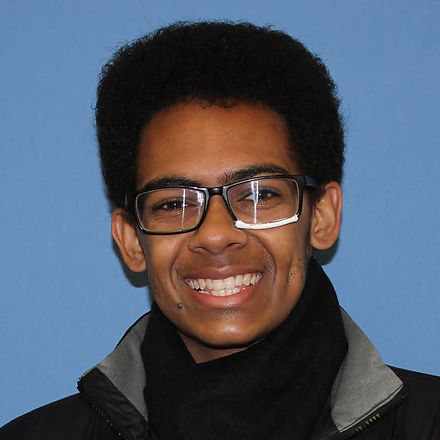

KEVIN LIU
Project Facilitator
JOSH WROBEL
Project CAD Lead/Head Officer

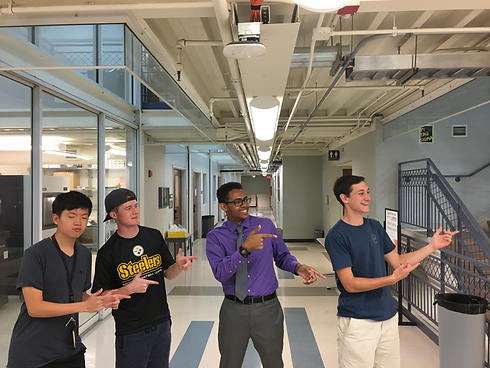
INTRODUCTION
Over the course of this semester (Fall 2018) we have had the pleasure of studying and applying the techniques associated with Design for Manufacturability to the reinvention and redesign of an existing product. In this project we undertook the task of modifying a Crank Action Hand Drill and have provided an outline of our design process in this website

ABOUT OUR PROJECT
In the Fall 2018 semester, we reverse-engineered a hand-crank drill for ME 270, producing an improved, ergonomic product with variable mechanical advantage.
ORIGINAL PRODUCT
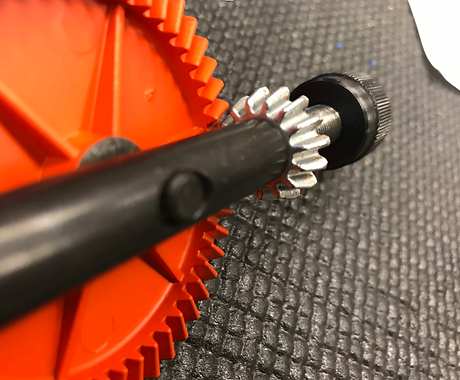

BILL OF MATERIALS (BOM) AND PRODUCT EXPLODED VIEW
BILL OF MATERIALS

CRANK ACTION HAND DRILL EXPLODED VIEW
Technical Specifications:
Weight: 8.8 ounces
Product dimensions: 2.4 x 2.6 x 9.3 inches
Material: Metal and Wood
Drill shank capacity: 1/4 inch
Bits and rotary tools capacity: 5/16 inch
Drive wheel diameter: 5/2 inch
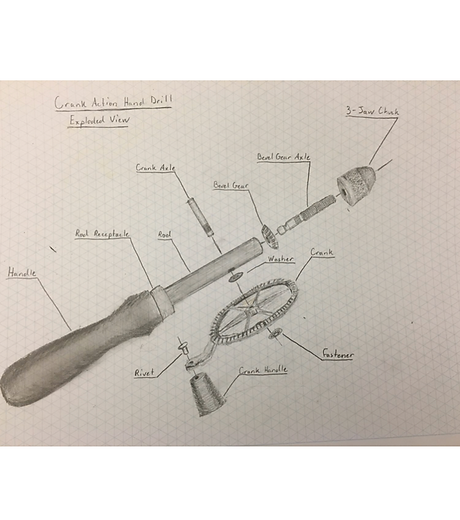
PRODUCT DESIGN TREE

COMPETITORS AND MARKET DATA
COMPETITORS
Due to the popularity of power tools, especially power drills, the crank action hand crank drill industry is relatively small. Along with Schröder, Fiskars and Weichuan also make hand crank drills. Since very few companies produce hand crank drills, Fiskars and Weichuan stand out as the primary competition with Schröder. The overall design of the Weichuan drill is quite similar to that of Schröder and has statistics that match the market data of Schröder quite closely. Though the design of Fiskars hand crank drill is quite unique with great variation compared to the drill produced by Schröder. As well, Fiskars is much larger compared to Schröder with a hand in multiple other products relating to the hand tool market. In consideration of these aspects, the market statistics of Fiskars are quite exploded compared to that of Schröder. Any other forms of competition with Schröder is manifested in the power drill industry in which DeWalt, Black & Decker, and Bosch are enormous contenders.
MARKET DATA
The power tools market was last valued at $27.19 billion in 2017. Since power tools have driven out the need for many hand tools such as a hand-crank drill, the market of hand tools is valued at a much smaller $16.04 billion. Screwdrivers (17%), tape measures, hammers, staple guns, and utility knives make up most of the sales volume of hand tools in the United States. Therefore, we estimate that hand crank drills makeup less than 1% (0.1%) of sales in the hand tool industry since most buyers buy electric drills instead of hand-crank drills. Schröder is a relatively small company in this market, so we are assuming that they sell about 10% of all hand-crank drills. They primarily sell through Amazon and other online retailers. Roughly, Schröder produces about $1.5 million - $3 million in sales of hand crank drills each year. Therefore, they sell somewhere in the range of 50,000 - 100,000 units per year at around $28 per unit.
The market value of hand tools is going to continue to increase over time due to the industrial nature of the world currently. The increase of commercial buildings and residential homes calls for the need of the increase of manufacturing of furniture, leading to the increase in need for hand tools. With that being said, the demand for hand-crank drills will be constant or decrease over time due to the overwhelming use of electric drills.
SOURCES
PRELIMINARY ESTIMATION OF MANUFACTURING COST AND DFM TECHNIQUES
ESTIMATE OF MANUFACTURING COST
One-third of the sales price is a reasonable estimate. According to The Mechanical Design Process, by George Ullman, “As a rule of thumb, for companies whose products are manufactured mainly in house and in high volume, … the selling price is approximately … three times the manufacturing cost” (319). Schröder has its own manufacturing facilities, and the Schröder Hand Drill has a relatively high number of customer reviews compared to other products sold by the same company. Therefore the estimated manufacturing cost is $8 to $9.
DESIGN ANALYSIS FOR DFM
Schröder sells a variety of drill chucks separate from their drills. To reduce cost, the drills come with the same drill bits Schroeder sells separately. Accordingly, Schröder has designed for proper assembly by making two different types of chucks, 5.103.9 and 5.104.9, that can both attach onto the same axle.
The handle is radially symmetric along a lengthwise axis, showing Schröder designed the handle for turning. The intervals between gear teeth have filleted edges, likely a design feature accommodating finishing with ball mills.
SOURCES
ORIGINAL PRODUCT (CAD)

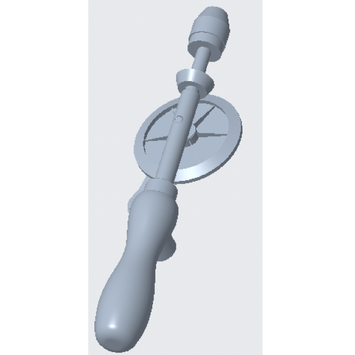
ANALYSIS OF APRIORI COST ANALYSIS FOR THE ORIGINAL PRODUCT
There were several discrepancies between the data input into aPriori and the actual parts.
The Handle (1), Rod Receptacle (2), Rod (3) were press-fit tightly. As a result, these three parts were not fully disassembled, and the CAD part that we input into aPriori modeled all three parts as one part.
In addition, the Handle (1) is made of wood, while the Rod Receptacle (2) and the Rod (3) are made of steel, causing further discrepancies between the simulation and the actual part.
The modeling of the gears is also unrealistic. The models of the Bevel Gear (4) and Crank (7) lack teeth, decreasing manufacturing cost. However, gears are usually manufactured via a sequence of different processes, and aPriori only allows one process to be assigned to a part. This results in a greatly inflated manufacturing cost.
The inaccuracy of the simulation is demonstrated by the simulated piece per part cost of $60.56 being much greater than the sales price of $27.87.
Despite the inaccuracies of the CAD models, the Crank (7) probably still has the highest actual piece per part cost. Gears require both precise and accurate manufacturing techniques to properly mesh. As well, the actual manufacturing of the Crank was most likely done through a series of manufacturing processes that could play a vital role to the overall cost of the part. However, due to the nature of aPriori, we were only able to analyze the cost of the crank using one manufacturing process which could adversely cause an inflated price estimate. Since our product is intended for low-volume production, the piece per part cost of the Crank (7) will remain high because of limitations on hard tooling. Therefore, for our reverse-engineered product, we should purchase as many gears as possible. Other specialized companies that have invested more into gear manufacturing machines could produce our gears at a cheaper cost.
If we have to produce gears in-house, they should first be sand-cast and then machined to proper tolerances. Sand-casting has lower investment costs than die casting and can quickly produce complex geometries, compared to machining, which requires time, complicated machining equipment, and high wages for skilled machinists.
While the piece per part cost is dominated by the Crank (7), the total capital investments are dominated by the Crank Handle (8), because it was simulated as an injection-molded part. Injection molding requires large amounts of product-specific investments, which are dominated by the cost of machining the dies. For low-production volumes, high investment costs are not sustainable. Therefore forming the Crank Handle (8) out of sheet metal could greatly decrease investment costs, because sheet metal forming does not require dies that can sustain the high pressures of injection molding.
In addition, the Crank Axle (6) could be attached to the Crank (7), to ease assembly. However, doing so would make the Crank (7) more complex, and it is already an expensive part. Therefore the benefit of such a change is ambiguous.
The fasteners used in the original product (the Rivet (9), the Washer (10), and the Fastener (11)) could also be eliminated and replaced with snap fits, which would ease assembly, especially because the fastening methods used in the original design are permanent. Permanent fastenings make assembly errors hard to reverse and also complicate assembly, disassembly and maintenance, potentially requiring more specialized tools and knowledge than snap fits.
While snap fits are complex and will significantly increase manufacturing costs, ease of maintenance, assembly, and disassembly have a direct and significant impact on customer satisfaction, as determined in our QFD.
Therefore, to minimize manufacturing cost and increase profits, gears should be mostly purchased from other companies, and gears produced in-house should be sand-cast and machined. Plastic parts should be replaced with sheet metal, and existing fasteners should be replaced with snap fits.